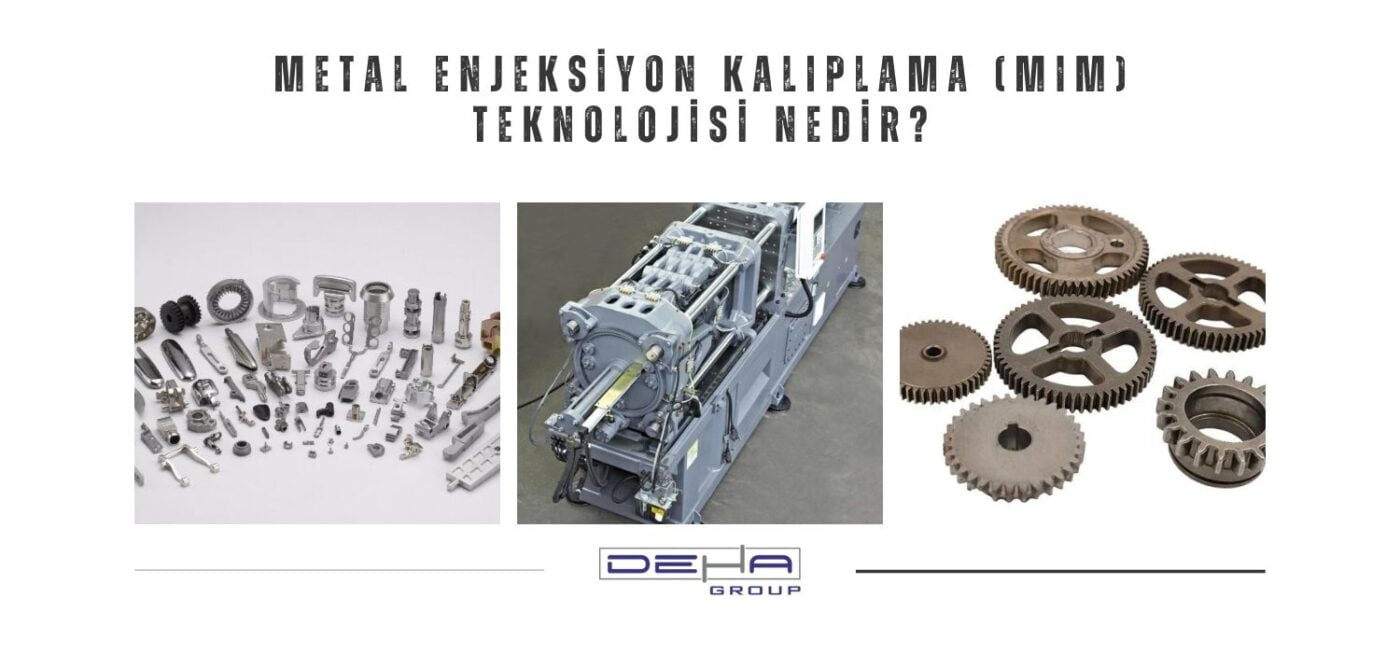
Metal Enjeksiyon Kalıplama (MIM) , metal tozları ve polimer bağlayıcıların karıştırılmasıyla oluşturulan bir hamurun enjeksiyon kalıplama yöntemiyle şekillendirilmesi ve ardından sinterlenerek yoğun metal parçalar elde edilmesi sürecidir. Bu yöntem, karmaşık geometrilere sahip küçük metal parçaların yüksek hassasiyet, mükemmel yüzey kalitesi ve üstün mekanik özelliklerle üretilmesini sağlar. MIM, otomotiv, havacılık, tıbbi cihazlar, elektronik ve tüketici ürünleri gibi çeşitli endüstrilerde yaygın olarak kullanılır.MIM, genellikle karmaşık geometrilere sahip küçük metal parçaların üretiminde kullanılır ve yüksek hassasiyet, mükemmel yüzey kalitesi ve yüksek mekanik özellikler sunar.
Metal Enjeksiyon Kalıplama (MIM) yöntemi, metal tozlarının polimer bağlayıcılar ile karıştırılarak oluşturulan bir hamurun, enjeksiyon kalıplama yöntemiyle şekillendirilmesi ve ardından sinterleme işlemiyle yoğun, yüksek performanslı metal parçalar elde edilmesi sürecidir. Bu teknoloji, karmaşık geometrik şekillere sahip küçük metal parçaların üretiminde büyük avantajlar sunar.
Hammadde Hazırlama (Feedstock Hazırlığı)
Metal Tozları: Yüksek saflıkta ve ince taneli metal tozları kullanılır. Bu tozlar, parçaların nihai yoğunluk ve mekanik özelliklerini belirler.
Bağlayıcılar: Polimer, mum ve diğer organik bileşikler gibi bağlayıcılar, metal tozlarını bir arada tutmak için kullanılır.
Karıştırma ve Granülasyon: Metal tozları ve bağlayıcılar homojen bir karışım elde etmek için karıştırılır. Bu karışım daha sonra enjeksiyon kalıplama makinelerinde kullanılabilir granüller haline getirilir.
Enjeksiyon Kalıplama
Kalıplama: Granüller, plastik enjeksiyon makinelerine benzer makinelerde, özel tasarlanmış kalıplara enjekte edilir. Bu aşamada, parçalar istenen geometrik şekli alır.
Kalıptan Çıkarma: Enjekte edilen parçalar kalıptan çıkarılır ve “yeşil parça” (green part) olarak adlandırılan, henüz bağlayıcılardan arındırılmamış bir forma sahip olur.
Bağlayıcı Uzaklaştırma (Debinding)
Kimyasal Debinding: Bazı bağlayıcılar kimyasal çözücüler kullanılarak uzaklaştırılır. Bu işlem sırasında parçalar daha gözenekli hale gelir.
Termal Debinding: Parçalar, termal işlemlerle ısıtılarak bağlayıcıların buharlaştırılması sağlanır. Bu işlem, bağlayıcıların tamamen uzaklaştırılması için kullanılır.
Sinterleme
Yüksek Sıcaklıkta Isıtma: Bağlayıcılardan arındırılmış “kahverengi parçalar” (brown part), yüksek sıcaklıklarda sinterleme işlemine tabi tutulur. Sinterleme, metal tozlarının birleşmesini ve yoğunlaşmasını sağlar.
Fırın Atmosferi: Sinterleme genellikle koruyucu bir atmosferde (örneğin, vakum, hidrojen veya inert gaz atmosferi) gerçekleştirilir, bu da oksidasyonu ve diğer olumsuz etkileri önler.
Son İşlemler (Post-Sintering Operations)
Isıl İşlemler: Parçaların mekanik özelliklerini iyileştirmek için ek ısıl işlemler uygulanabilir.
Yüzey İşlemleri: Parçaların yüzey kalitesini artırmak veya estetik amaçlarla çeşitli yüzey işlemleri (örneğin, kaplama, parlatma) uygulanabilir.
Talaşlı İmalat: Gerekirse, hassas toleranslar veya ek özellikler için sonrasında talaşlı imalat işlemleri yapılabilir.
Karmaşık Geometriler: MIM, karmaşık şekilli metal parçaların üretimini mümkün kılar.
Yüksek Hassasiyet ve Tekrarlanabilirlik: MIM, yüksek hassasiyet ve tekrarlanabilirlik sunar, bu da büyük hacimli üretimlerde tutarlı kalite sağlar.
Malzeme Çeşitliliği: Paslanmaz çelik, titanyum, nikel bazlı alaşımlar ve daha birçok metal alaşım MIM sürecinde kullanılabilir.
Yüksek Mekanik Özellikler: MIM ile üretilen parçalar, döküm veya talaşlı imalat yöntemlerine kıyasla daha üstün mekanik özelliklere sahip olabilir.
Maliyet Verimliliği: Özellikle büyük hacimli üretimlerde MIM, daha düşük üretim maliyetleri ve daha az malzeme israfı sağlar.
Otomotiv Endüstrisi: Karmaşık motor parçaları, dişliler ve diğer yüksek hassasiyet gerektiren bileşenler.
Havacılık ve Savunma: Hafif ve dayanıklı parçalar, yüksek sıcaklık dayanımı gerektiren bileşenler.
Tıbbi Cihazlar: Diş implantları, ortopedik implantlar ve cerrahi aletler.
Elektronik: Küçük ve hassas elektronik bileşenler, konnektörler ve sensörler.
Tüketici Ürünleri: Gözlük çerçeveleri, saat parçaları, mücevherler ve diğer yüksek kaliteli tüketici ürünleri.
MIM yöntemi, modern üretim teknolojileri arasında önemli bir yer tutmakta olup, birçok endüstride yenilikçi çözümler sunmaktadır. Karmaşık ve küçük metal parçaların yüksek kalite ve düşük maliyetle üretilmesini sağlayarak, üretim süreçlerini daha verimli hale getirmektedir.
Metal Enjeksiyon Kalıplama (MIM) teknolojisini diğer metal işleme ve üretim teknolojilerinden ayıran özellikler, bu yöntemin kendine özgü avantajlarını ve uygulama alanlarını belirler. İşte MIM teknolojisini öne çıkaran başlıca özellikler:
Karmaşık Geometrilerin Üretimi
MIM, karmaşık şekilli ve detaylı metal parçaların üretimini mümkün kılar. Geleneksel döküm, talaşlı imalat veya metal şekillendirme yöntemleriyle üretilemeyecek kadar karmaşık tasarımlar MIM ile kolayca üretilebilir.
Yüksek Hassasiyet ve Tekrarlanabilirlik
MIM, yüksek hassasiyet ve tekrarlanabilirlik sunar. Üretilen parçalar, dar tolerans aralıklarında ve tutarlı kaliteyle üretilir, bu da seri üretimde büyük avantaj sağlar.
Malzeme Çeşitliliği
MIM, geniş bir malzeme yelpazesiyle uyumludur. Paslanmaz çelik, titanyum, nikel bazlı alaşımlar, bakır ve diğer metal tozları kullanılarak çeşitli mekanik ve kimyasal özelliklere sahip parçalar üretilebilir.
Yüksek Mekanik Özellikler
MIM ile üretilen parçalar, yüksek yoğunluk ve mükemmel mekanik özellikler sunar. Sinterleme işlemi, parçaların yoğunluğunu artırarak, mukavemet ve dayanıklılık gibi mekanik özelliklerini iyileştirir.
Düşük Malzeme İsrafı
MIM, malzeme israfını minimize eder. Enjeksiyon kalıplama süreci, malzemenin büyük bir kısmını kullanır ve bu da verimliliği artırır. Talaşlı imalat gibi yöntemlerle kıyaslandığında, MIM ile üretilen parçalar daha az malzeme israfına neden olur.
Büyük Hacimli Üretim
MIM, büyük hacimli üretim için idealdir. Yüksek üretim hızları ve düşük parça maliyetleri ile seri üretim süreçlerinde önemli avantajlar sunar.
Yüzey Kalitesi
MIM ile üretilen parçalar, yüksek yüzey kalitesi ve pürüzsüzlük sunar. Bu, ek yüzey işlemlerine olan ihtiyacı azaltabilir veya tamamen ortadan kaldırabilir.
Parça Birleştirme İhtiyacını Azaltma
MIM, tek bir parça olarak üretilebilecek karmaşık şekilli bileşenlerin tasarımını mümkün kılar. Bu, birden fazla parçanın montajını ve birleştirilmesini gerektiren süreçleri ortadan kaldırarak üretim verimliliğini artırır.
Yüksek Ölçeklenebilirlik
MIM, küçük prototiplerden büyük ölçekli seri üretime kadar kolayca ölçeklenebilir. Bu, ürün geliştirme süreçlerinde ve pazara hızlı giriş yapma konusunda büyük bir avantaj sağlar.
Çevresel Etki
MIM, enerji verimliliği ve düşük malzeme israfı sayesinde çevresel etkiyi minimize eder. Ayrıca, kullanılan malzemelerin geri dönüştürülebilir olması, çevre dostu bir üretim süreci sunar.
Diğer Teknolojilerle Karşılaştırma
Döküm: Döküm yöntemleri büyük ve basit şekilli parçalar için uygundur, ancak MIM kadar karmaşık ve detaylı parçaların üretiminde sınırlıdır. Ayrıca, döküm süreçleri daha fazla malzeme israfına ve düşük yüzey kalitesine yol açabilir.
Talaşlı İmalat: Talaşlı imalat, yüksek hassasiyet sunar ancak karmaşık geometrilerin üretimi zordur ve malzeme israfı yüksektir. MIM, talaşlı imalata göre daha az malzeme israfı ve daha yüksek verimlilik sağlar.
Metal Şekillendirme: Metal şekillendirme yöntemleri, levha metal işlemede etkilidir ancak karmaşık üç boyutlu parçaların üretiminde sınırlıdır. MIM, bu açıdan daha esnek ve kapsamlı çözümler sunar.
Eklemeli Üretim (3D Baskı): 3D baskı, prototip üretiminde ve küçük ölçekli üretimlerde avantajlıdır ancak büyük hacimli üretimlerde MIM kadar ekonomik değildir. Ayrıca, 3D baskı ile elde edilen parçaların mekanik özellikleri ve yüzey kalitesi MIM ile üretilen parçalar kadar iyi olmayabilir.
Metal Enjeksiyon Kalıplama (MIM) teknolojisi, karmaşık ve hassas metal parçaların yüksek hacimli üretiminde sunduğu benzersiz avantajlarla öne çıkar. Bu özellikler, MIM’i birçok endüstride tercih edilen bir üretim yöntemi haline getirir.